At present, the world's advanced manufacturing technologies continue to rise, the application of ultra-high-speed cutting, ultra-precision machining and other technologies, the rapid development of flexible manufacturing systems, and the continuous development of computer integrated systems have placed higher demands on numerical control processing technology. Today's CNC machine tools are moving in the following directions.
1. High-speed, high-precision speed and accuracy are two important indicators of CNC machine tools, which are directly related to processing efficiency and product quality. At present, the numerical control system uses a processor with a higher number of bits to increase the basic operation speed of the system. At the same time, ultra-large-scale integrated circuits and multi-microprocessor architectures are used to improve the system's data processing capabilities, that is, to increase the speed and accuracy of interpolation operations. The straight-line servo feed method that directly drives the machine table using a linear motor has superior high-speed and dynamic response characteristics. Using feedforward control technology, the tracking lag error is greatly reduced, thereby improving the machining accuracy of corner cutting.
In order to meet the requirements of ultra-high-speed machining, CNC machine tools use a structure in which the spindle motor and the machine tool spindle are combined to realize the integration of the variable-frequency motor and the machine tool spindle. The bearings of the spindle motor use magnetic bearings, hydrostatic hydrostatic bearings, or ceramic rolling bearings. form. At present, ceramic tools and diamond-coated tools have begun to find application.
2. Multi-functional machining center equipped with automatic tool changer (up to 100 magazines), capable of simultaneous milling, boring, drilling, turning, reaming, reaming and tapping on the same machine Threads and other processes, modern CNC machine tools also use a multi-spindle, polyhedron cutting, that is, different parts of a part at the same time different ways of cutting. Due to the multi-CPU architecture and hierarchical interrupt control, the CNC system can perform part processing and programming on a single machine at the same time, achieving the so-called “front-end processing, background editingâ€. In order to meet the requirements of the flexible manufacturing system and the computer integrated system, the numerical control system has a long-distance serial interface, and even can be networked to realize the data communication between the CNC machine tools, and can also directly control multiple CNC machine tools.
3. Intelligent modern CNC machine tools will introduce adaptive control technology, automatically adjust the operating parameters according to changes in cutting conditions, so that the best working conditions can be maintained during the process, resulting in higher processing accuracy and a smaller surface roughness. It can also increase the tool life and equipment production efficiency. With self-diagnosis and self-repair functions, the system performs self-diagnosis and inspection of the CNC system itself and various connected devices at any time during the entire working state. Once a fault occurs, measures such as downtime are used immediately, and a fault alarm is issued to indicate the location and cause of the fault. It is also possible to automatically bring the faulty module offline and switch on the spare module to ensure the requirements of an unattended working environment. In order to achieve higher fault diagnosis requirements, the trend is to use artificial intelligence expert diagnosis system.
4. CNC programming automation With the development of computer application technology, the current CAD/CAM graphics interactive automatic programming has been more commonly used, is a new trend in the development of CNC technology. It is the use of CAD to draw the parts of the processing pattern, and then through the computer tool path data calculation and post-processing, so as to automatically generate NC parts processing program to achieve the integration of CAD and CAM. With the development of CIMS technology, CAD/CAPP/CAM integrated automatic programming has emerged. The biggest difference between CADS/CAM and CAM system programming is that the process parameters needed for programming do not have to be manually involved, directly from the system. Within the CAPP database.
5. Reliability Maximization The reliability of CNC machine tools has always been the main indicator of the user's concern. The numerical control system will use higher integrated circuit chips and utilize large-scale or ultra-large-scale dedicated and hybrid integrated circuits to reduce the number of components and improve reliability. Through the hardware function software, in order to meet the requirements of various control functions, at the same time using the hardware structure of the machine body modularization, standardization, generalization and serialization, making it not only improve the hardware production volume, but also facilitate the organization of production and quality checks. It also enables diagnostics, online diagnostics, offline diagnostics and other diagnostic programs to automatically perform fault diagnosis and alarms on the hardware, software, and various external devices in the system. Use alarm prompts to eliminate faults in a timely manner. Use fault-tolerant technology to adopt "redundant" design for important components to achieve fault self-recovery; use various test and monitoring techniques to produce overtravel, tool damage, interference, power failure, etc. In case of an accident, the corresponding protection is automatically performed.
6. The miniaturization of the control system The miniaturization of the CNC system facilitates the integration of the machine and the electric device. At present, ultra-large-scale integrated components and multi-layer printed circuit boards are mainly used, and three-dimensional mounting methods are used to enable high-density mounting of electronic components and reduce the space occupied by the system. The replacement of traditional cathode ray tubes with a new type of color liquid crystal thin display will further miniaturize the numerical control operating system. In this way, it can be easily installed on the machine tool and it is easier to use the CNC machine tool.3D printing on the pen machine is mainly used in 3 d printing pen, is made from a special custom Dc Gear Motor, mainly used in 3 d printing pen, pen 3 d printing machine has been updated three generations according to the requirements of product.
3D Printing Motor product introduction:
The 3D Printing Motor is based on the deceleration Motor, coupled with supporting gears and ball bearings.The role of the gear reducer is to provide lower speed and greater torque.At the same time, gear box different deceleration ratio can provide different speed and torque.It's mostly rolling.
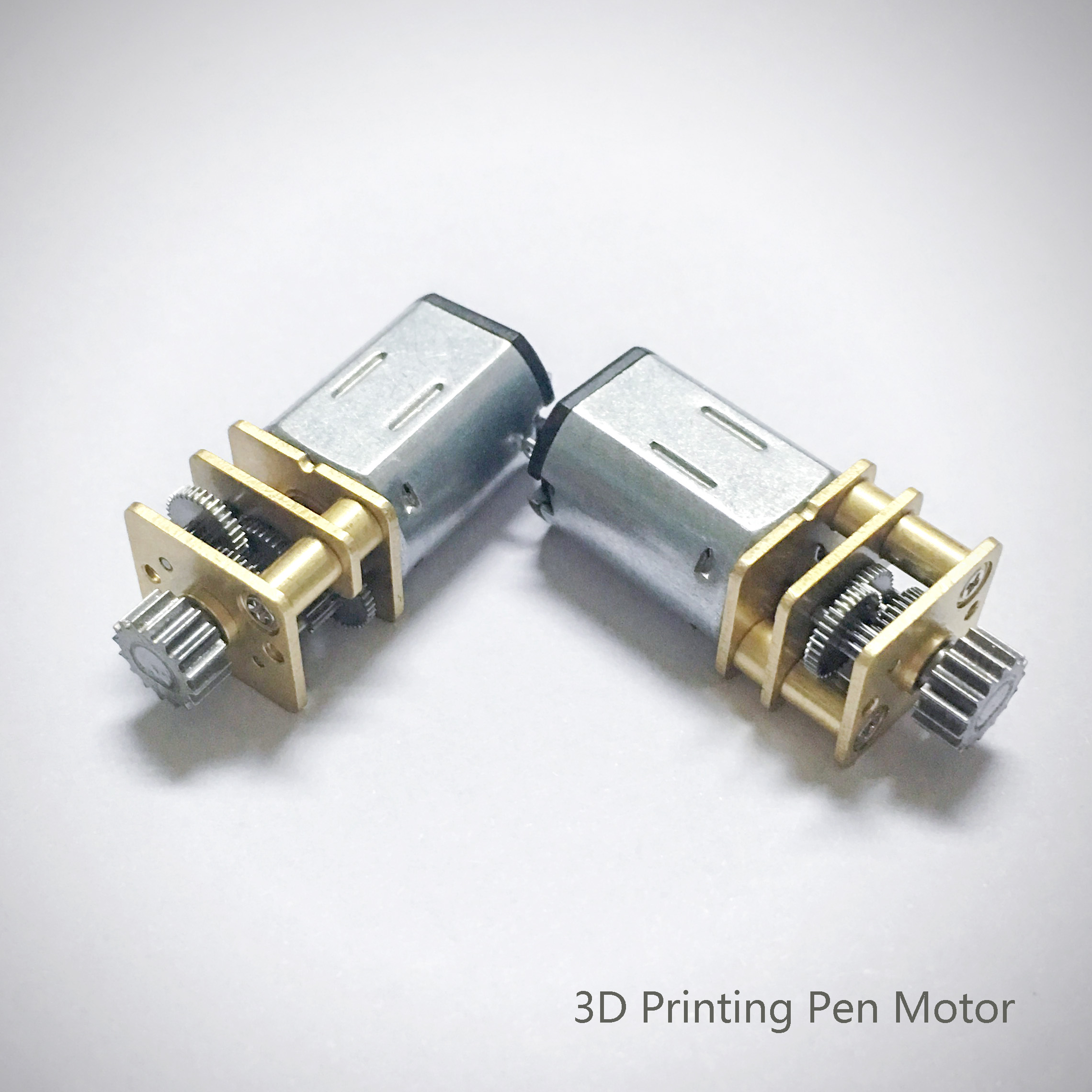
Features: 3D Printing Motor, small size, large torque, low noise, durable, low energy consumption, customized power design, convenient installation and maintenance;
Simplify design and save space.
Features: usually used financial equipment, office equipment, electronic locks, wireless charger, remote control toys, precision instruments and meters, automobile industry, medical equipment, consumer electronics, household appliances, electric glass doors and Windows, etc., wide application range
Method of use: the best stable in horizontal plane, installed on the 3D Printing Motor output shaft parts, cannot use a hammer to knock, knock prone to press into the 3D Printing Motor drive, may cause damage to internal components, and cannot be used in the case of blocked.
Operating temperature range:
3D Printing Motor should be used at a temperature of -10~60℃.
The figures stated in the catalog specifications are based on use at ordinary room temperature catalog specifications re based on use at ordinary room temperature (approximately20~25℃.
If a 3D Printing Motor is used outside the prescribed temperature range,the grease on the gearhead area will become unable to function normally and the motor will become unable to start.Depending on the temperature conditions ,it may be possible to deal with them by changing the grease of the motor's parts.Please feel free to consult with us about this.
Storage temperature range:
3D Printing Motor should be stored ta a temperature of -15~65℃.
In case of storage outside this range,the grease on the gearhead area will become unable to function normally and the motor will become unable to start.
Service life:
The longevity of 3D Printing Motor is greatly affected by the load conditions , the mode of operation,the environment of use ,etc.Therefore,it is necessary to check the conditions under which the product will actually be used .The following conditions will have a negative effect on longevity.Please consult with us should any of them apply.â—Use with a load that exceeds the rated torque
â—Frequent starting
â—Momentary reversals of turning direction
â—Impact loads
â—Long-term continuous operation
â—Forced turning using the output shaft
â—Use in which the permitted overhang load or the permitted thrust load is exceeded
â—A pulse drive ,e.g.,a short break,counter electromotive force,PWM control
â—Use of a voltage that is nonstandard as regards the rated voltage
â—Use outside the prescribed temperature or relative-humidity range,or in a special environment.
â—Please consult with us about these or any other conditions of use that may apply,so that we can be sure that you select the most appropriate model.
when it come to volume production,we're a major player as well .each month,we rurn out 600000 units,all of which are compliant with the rohs directive.Have any questions or special needed, please contact us, we have the engineer group and best sales department to service to you Looking forward to your inquiry. Welcome to our factory.
3D Printing Motor,3D Printing Gear Motor,3D Printing Pen Motor,3D Printing Spindle Motor
Shenzhen Shunchang Motor Co., LTD. , https://www.scgearmotor.com